Almost a year after the end of my PhD and starting my employment with Constellium, I am reflecting on my doctoral experience and the collaboration with industry.
I started my Engineering and Physical Sciences Research Council (EPSRC) Industrial Cooperative Award in Science and Engineering (ICASE) PhD in October 2017. Previously, I completed an MEng in mechanical engineering and an MSc in nanoscience and nanotechnology.
Through the ICASE program I had the opportunity to combine my 2 main interests: my passion for science and the industrial hands-on experience.
Research
My PhD was focused on the characterisation and understanding of the microstructure development in high-strength automotive aluminium alloys. The use of aluminium in the automotive industry has increased during the last decades, since aluminium alloys show many advantages compared to more traditional structural materials. Aluminium’s light weight can result in a total vehicle weight reduction and enhance the reduction of carbon dioxide emissions and fuel consumption.
Many automotive parts are extruded and since extrusion is a complex procedure, involving various parameters, there is still much potential for further investigation into how these parameters affect crystallographic orientation (texture) and final mechanical properties. By applying my work within the STEP (Strain Enhanced Precipitation) Prosperity Partnership program in partnership with Brunel University London we are aiming to provide ultra-high strength alloys to further lightweight structural aluminium components, such as crash management systems, by up to 30%.
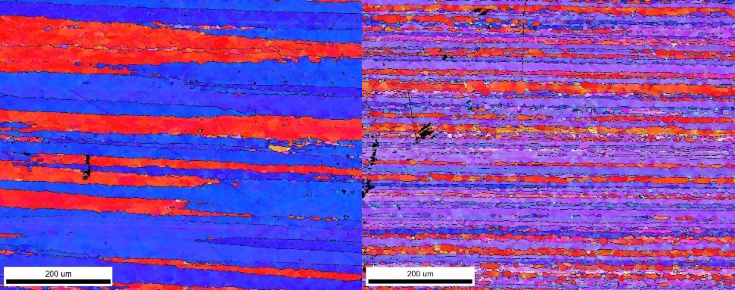
2 microstructure images showing the comparison of crystallographic orientation between 2 extruded profiles in a magnesium and silicon aluminium alloy. Image a) is from a round bar extrusion and shows relatively thick banding of 2 distinct orientations. Image b) is from a flat profile extrusion and shows a finer, fibrous structure which includes more variation in orientation. Differences in grain structure and different crystallographic orientations will contribute different levels of strengthening, and consequently will impact the mechanical properties in the final product. Credit: Constellium
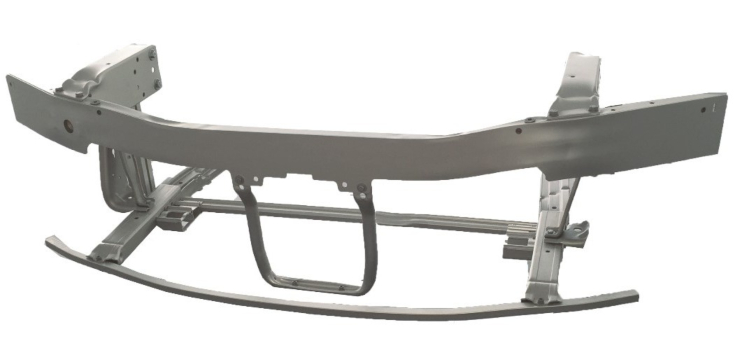
Constellium’s Crash Management System solutions enable maximum lightweight construction. Credit: Constellium
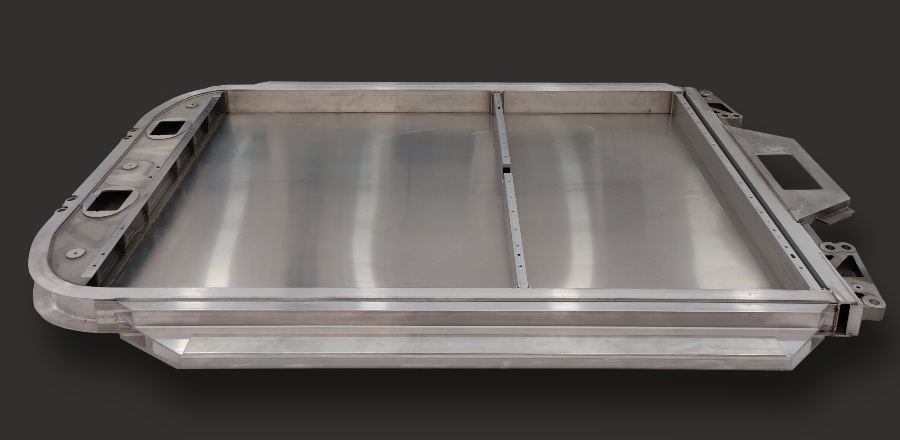
Strong, lightweight, crash- and intrusion-resistant battery enclosures for electric vehicles, from collaborative research and development projects led by Constellium. Credit: Constellium
Collaboration
During my PhD, I worked closely with Constellium, at their University Technology Centre in Brunel University London, part of their Automotive Structures and Industry Business Unit. I was involved in the alloy development over different scales, that is, from microstructural investigation on state-of-the-art equipment, to prototyping at 1:1 scale on an industrial size extrusion line located in the Advanced Metal Casting Centre building at Brunel University.
Within the framework of the collaboration between the Brunel Centre for Advanced Solidification Technology and Constellium, I also had the chance to be exposed to and trained in industrial practices and processes of a global leader in the aluminium industry. Moreover, with the support from my academic supervisors I had the opportunity to showcase my research in a series of workshops and conferences. This helped me to broaden my fundamental view and build a network of fellow scientists. The people I met both from Constellium and Brunel sides were of really great quality and in many cases acted as mentors to me.
After PhD
For me, the next step after finishing my PhD was to work in the industry and I have been extremely lucky to be the first ICASE student onboarding to Constellium’s research and development (R&D) Metallurgy team in order to continue working and developing the company’s alloy portfolio. Specifically, with my contribution to the STEP project I am working on developing a new generation of high-performance aluminium alloys with ultra-high strength, good ductility, high crashworthiness and high thermal conductivity. For both me and Constellium this comes as the next step of a collaboration started 4 years ago, with me beginning my industrial career with an arsenal of scientific knowledge on material science and characterisation, and the practical aspect of aluminium processing.
Summary
From my experience, an ICASE PhD is a great opportunity for those wishing to be exposed to both academia and industry. The combination of fundamental knowledge with the industrial experience that ICASE provides can be a springboard not only to a career in the industry but it’s also a great way for those wishing to stay in academia to broaden their perspectives, especially in a field like engineering. Now, that my PhD journey has finished, I can say that the program was an excellent fit for me!
Follow Chrysoula Tzileroglou on LinkedIn.