I am an Industrial Cooperative Award in Science and Engineering (ICASE) PhD student working with industry on the research and development of next generation liquid hydrogen fuel tanks. The experimental modelling of liquid sloshing is essential for effective design and certification of a liquid hydrogen storage and fuel delivery system. My research can help inform this design.
After completing an MEng in mechanical engineering at Heriot-Watt University (Edinburgh campus) in 2021, I had the opportunity to kickstart a career in research through an Engineering and Physical Sciences Research Council (EPSRC) ICASE PhD at the University of Plymouth.
I was attracted to the ICASE scheme due to the link with the industrial partner Airbus and the opportunity to participate in a three month placement at Airbus’ offices.
Next generation aircraft
The aviation industry is developing environmentally friendly next generation aircraft, to reduce its contribution to global greenhouse gas emissions. Thus, Airbus is aiming for aircraft powered by liquid hydrogen (LH2).
The specific focus of my PhD is on the technical challenge of sloshing within a LH2 fuel tank. Sloshing is simply the motion of liquid within the fuel tank. The challenge with sloshing in LH2 fuel tanks is describing how this motion effects the temperature and pressure inside the fuel tank. Understanding this interaction is important for effective design and certification of liquid hydrogen storage and fuel delivery systems.
Think about what happens to the temperature of your cup of tea when you leave it on your desk. Heat flows from hot to cold, thus your cup of tea cools down because of the cooler temperature of the surrounding air. This is the second law of thermodynamics – heat flows from hot to cold.
In a LH2 fuel tank the same effect occurs, however, in this case the LH2 is colder than the gas above it. Therefore, the effect occurs in the opposite direction and the warmer gas transfers heat into the cooler liquid. This is depicted in the schematic below. This effect is magnified significantly when the liquid is moving (sloshing) due to the mixing between the two phases. As energy or heat is transferred into the liquid the pressure of the gas decreases and the liquid temperature increases, this can lead to issues with fuel management and fuel extraction into the engine.
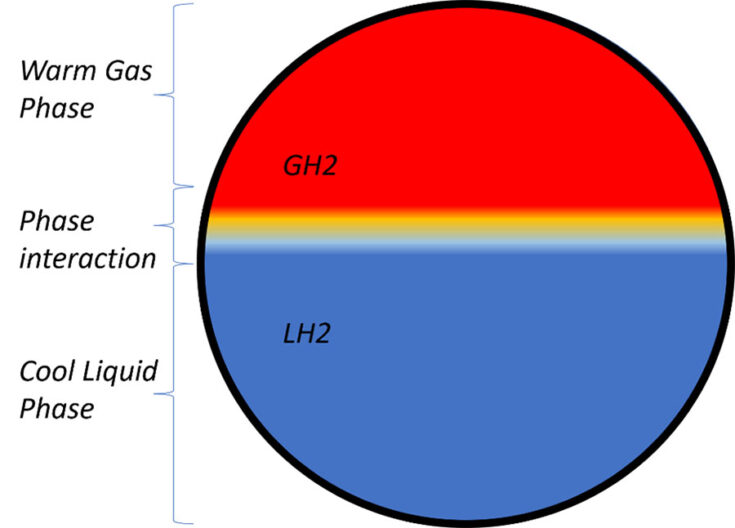
Image two: schematic portraying temperature interaction between phases in a LH2 fuel tank.
Credit: Stuart Colville
Sloshing behaviour
To address this problem, I am undertaking experimental research to better understand the sloshing behaviour in LH2 fuel tanks. Together with Airbus we have developed a scaled down, simplified geometry of an LH2 fuel tank, as shown in images three and four. I perform experiments to characterise the sloshing fluid motion as this tank is accelerated. I characterise the sloshing behaviour through the fluid position and velocity. These are extracted from images captured with a high-speed camera. Images three and four described are from experiments using water and air at room temperature and pressure.
Furthermore, I am developing a tank which can be pressurised. The aim of this follow-up study is to develop an understanding of how the fluid motions I have characterised previously, impact the pressure and temperature in the fuel tank. These experiments will help to inform design and future experimental testing with LH2. This experimental setup incurs higher costs. Without the additional funding provided through the ICASE scheme these more complex experiments would not be possible.
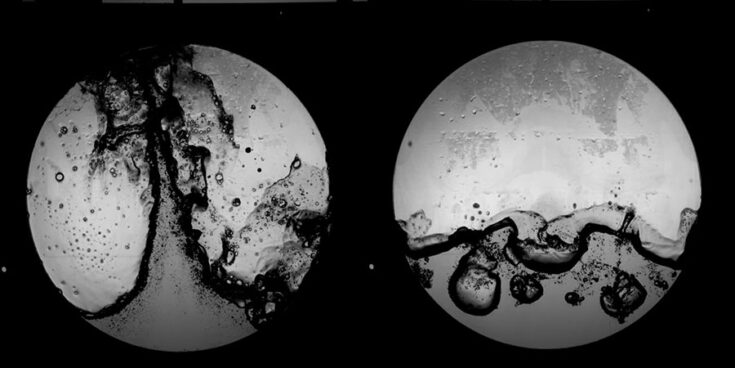
Image three (left) displays wave breaking, image four (right) displays air being entrained within the water, this can occur at high tank accelerations.
Credit: Stuart Colville
Industry collaboration
The collaborative effort between the University of Plymouth and Airbus to date has strengthened the relationship between the two partners, whilst also helping to deliver industry-relevant research. In one case my experiments have helped validate Airbus’ computational models. This specific test case is displayed in the images below. It shows the fluid travelling around the circumference of the geometry before impacting the liquid column on the opposite side. This phenomenon had been captured computationally but my tests could show it physically occurring in the tank. This has helped to build confidence in their ability to simulate fluid flow in the specific geometry.
The involvement of industry within my PhD has enhanced my learning experience by providing an industry point of view. This has helped to guide me through the course of my PhD and ensure my research is industry relevant. As I reach the second half of my ICASE PhD journey I am excited for what lies ahead and to apply the transferrable skills I have learned to new workplaces.
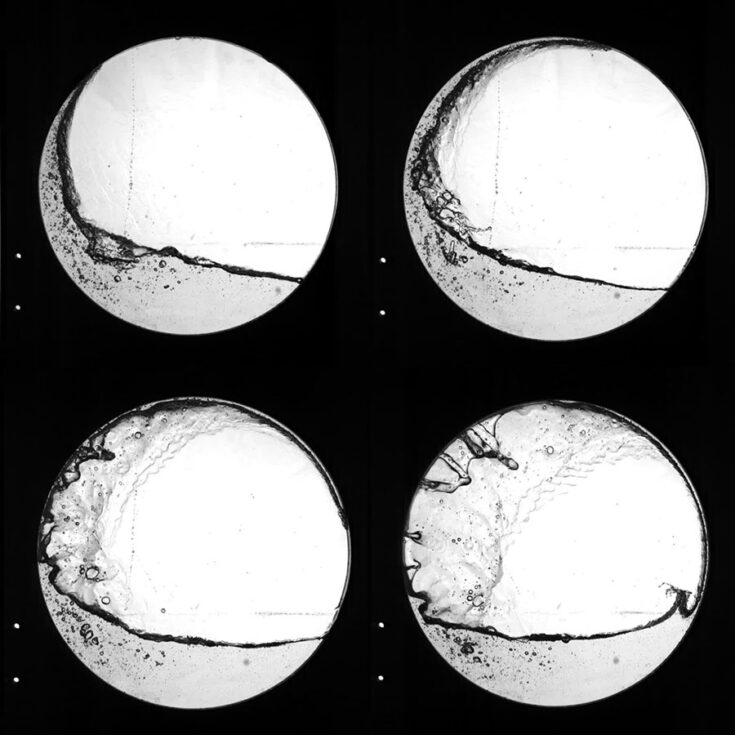
Fluid jet displayed travelling around left-hand side of the geometry circumference (images five (top left), six (top right) and seven (bottom left)) before impacting the liquid column on the right-hand side (image eight (bottom right)).
Credit: Stuart Colville
Here are two YouTube videos of horizontal sloshing and vertical acceleration sloshing.
Top image: Image one: sloshing liquid impacts tank roof under high acceleration. Credit: Stuart Colville